On Saturday, January 9th eight Houston MG Car Club members and a couple guests gathered at Rich Colwell’s house for a tech session on replacing the differential in an MGA. One of the guests was Mike Rouse, a member of the local Triumph club and very, let me say it again, very knowledgeable about British car differentials. He added much to the discussion and knowledge exchange.
Following a few stories about the how and why of Rich’s desire to replace
the differential in one of his two MGA’s, the work and teaching began. But first let me share Rich’s story. A while back he and Pete Sandy where on a drive where Pete’s MGA was cruising along at 70 MPH at about 3500 RPM, while Rich’s MGA was working hard at 4300 to 4400 RPM. The engines in our MG’s are more than capable of handling the higher RPM’s but there is no doubt Pete was having a much more enjoyable/quieter ride. After discussing with Pete why his car was cruising along so comfortably, Rich decided to make the swap, replacing his original 4.3:1 differential with a 3.9:1. About 5 years ago, Rich bought a
3.9:1 diff. from Dave Griffiths (another HMGCC member). It could have been an easy substitution, but the 3.9:1s' "sun gears" had 10 splines on them (for 1500 MGA), while Rich's MGA half axles had 25 splines (late 1600 MGA). Thus, the sun gears, planet gears, and planet gear shaft from the 4.3:1 diff. (along with new bearings and thrust washers) were installed into the 3.9:1 pumpkin. Saturday was the day to make the swap.
So what did I learn on Saturday.
- That a differential is often called a pumpkin. (I suppose it is because it looks like one.)
- Our LBC’s are not only tough machines, all things considered they are pretty simple in design.
- A 1000th of an inch matters.
- Having the right tool can make all the difference. And Rich has many, many tools. His garage is very well equipped, even with very unique and custom made tools he has had for years.
- Also, Rich is now the keeper of the Club’s tool loan program. One of the great benefits of membership is the ability to get your hands on those specialized tools. For more information click HERE.
- A great garage with plenty of room to work is a blessing.
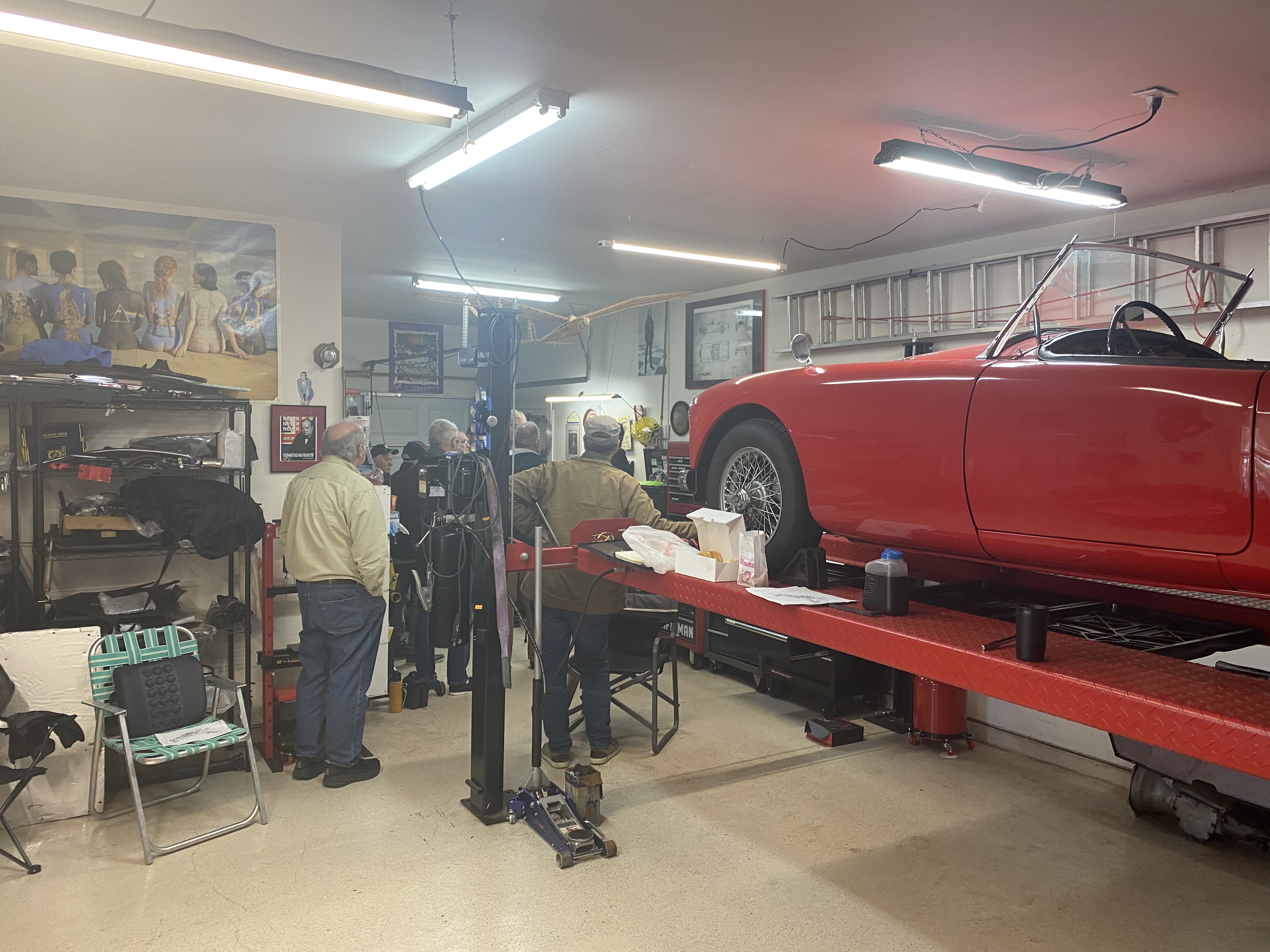
- There is a tremendous amount of knowledge in our club. And the axiom that two minds are better than one is really true (Thanks again to Mike Rouse).
- If you have a problem with your MG or are thinking about an upgrade, don’t hesitate to ask fellow club members. They are more than willing to share their knowledge and lessons learned.
- That said, it is always good to have an expert on hand who has years and years of experience. I think Mike Rouse has made it his life mission to learn everything there is to know about the differentials of LBC’s. His
expertise was invaluable. It also kept Rich from making mistakes.
- Having a shop manual and the knowledge to do the work is very different than actually being able to do the work. Perhaps because it is written in British instead of English. As often occurs, there is both art and science to making an MG hum.
- Rich had to fabricate a special tool to tighten up/torque the flange nut to the input shaft. It was comprised of two1-1/2" long 5/16" bolts welded to 1/2 angle iron. With the bolts inserted into 2 of the flanges 4 holes, it provided a method of holding the shaft in one position while torqueing. The car is now back on the road, and much quieter at freeway speeds.
- Rebuilding a differential properly takes up to 40 man hours.
- If the differential goes on my car, I am sending it to an expert to have the work done. I have pretty much determined that is the case for anything in the powertrain of the car. Too easy for me to screw it up.
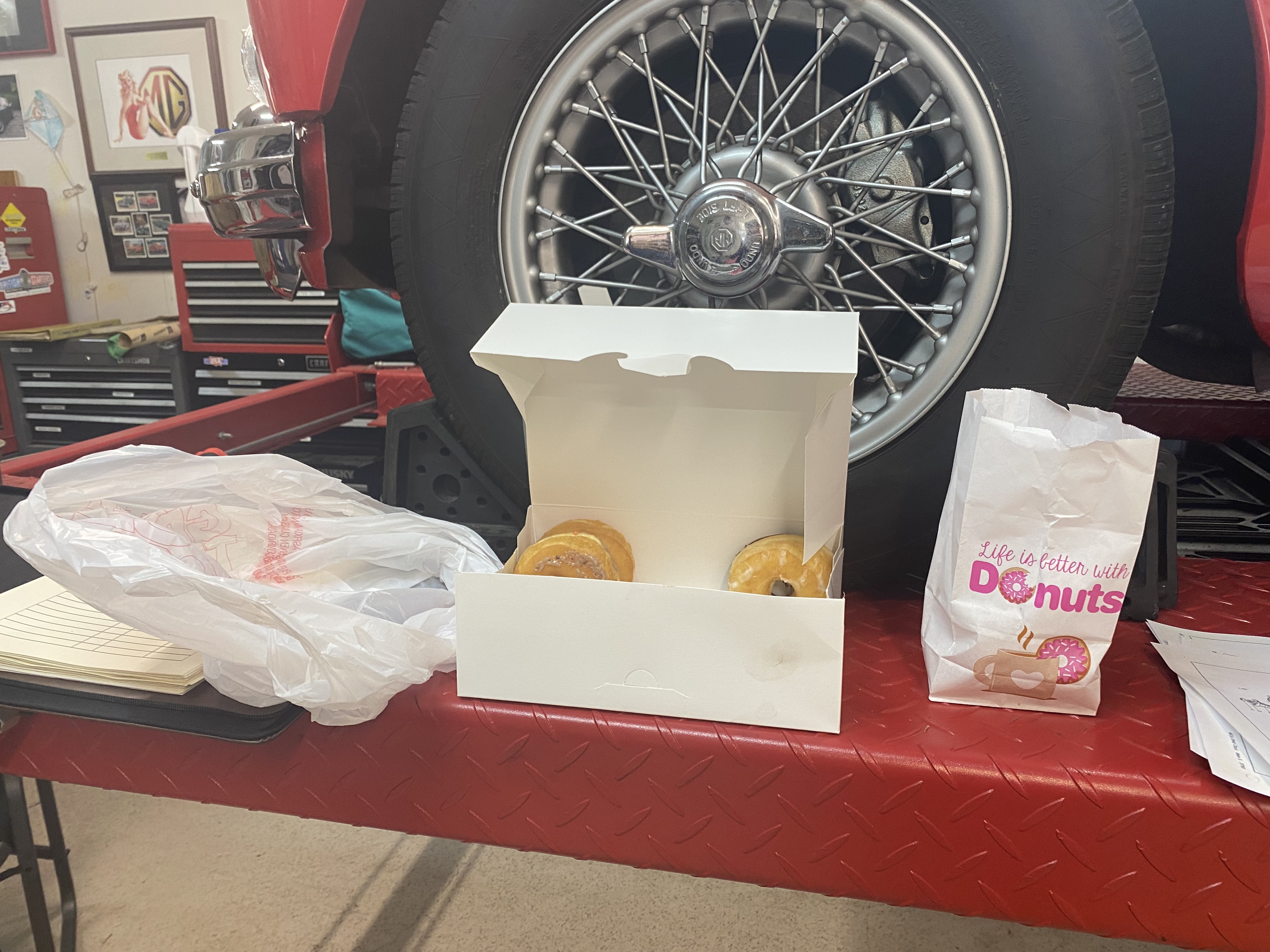
Oh yea, one more bonus learning… MG owner’s really are the friendliest folks on the planet. If you own an MG, actually even if you don’t but would like to, and you aren’t a member of the Club what are you waiting for? And to those of you who haven’t renewed for 2022 don’t miss out, your membership will expire at the end of February.
To watch a video of this and our other tech sessions click HERE
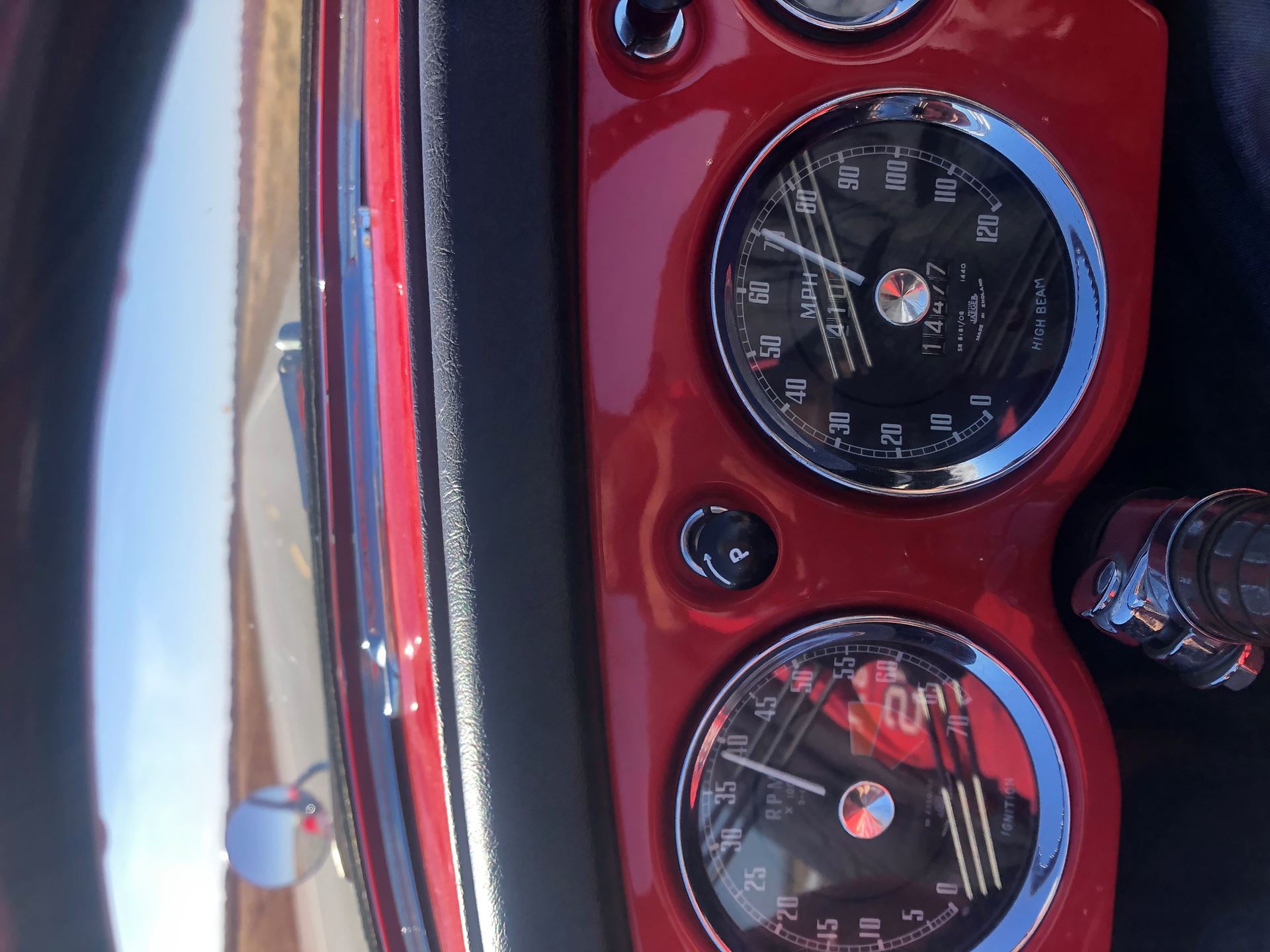
UPDATE From Rich: The modification works well. We went out for a nice drive today. In fourth gear I am at 3800 rpm versus 4450 or so with the old diff. While I feel a loss of acceleration in 2nd gear, it is easily overcome by higher revs. For Houston roads, it is a nice trade off. While at 4450 rpm, i know that i was not pushing the car, the new feeling is better, and i think on long trips will be more relaxing.
PS: my tool for torqueing down the diff. input flange nut, I topped out at 150 ft.-lbs., bending the tool. But was able to achieve 10 in.-lbs unloaded, not the 12 asked for, but I am not going to worry about it. At that level, it may be in the noise